

The 3D Contoured Groove Geometry

Creating the Spine Curve
The 3D Contoured Groove is best programmed by defining the Spine Curve. The Spine Curve is located at the bottom center of the groove. The Spine Curve is created from the surface edges located at the bottom of the groove. The following steps are performed. Also, refer to the illustration below.
- 3D Curves are created from the surfaces located on the side wall of the groove. More specifically, new curves are created from all edges located at one side and at the bottom of the groove.
- These curves are then merged to form one curve that runs the entire length of the groove at its base on one side.
- The 3D curve is then offset inward, toward the center of the groove, by 0.0725″ which is exactly one-half of 0.145”, the actual width of the groove. This becomes the Spine Curve.
- The new offset curve is positioned at the mid-way of the groove and at the bottom. We are calling this the Spine Curve shown in red in the illustration below.

Creating the 2½ Axis Engraving Operation
The Cutting Parameters include a global tolerance of 0.001”. The location of Cut Geometry (i.e., the spine curve) is set to At Bottom. This is the bottom of the cut. The Cut Depth, Rough Depth, Finish Depth, Rough Depth/Cut, and Finish Depth/Cut are all set to zero. This means that the cutter will follow the spine curve and not cut any deeper than that. The Cut Parameters tab of the Engraving operation is shown below.

Engraving Toolpath Entry and Exit Parameters
For display and illustration purposes, we see that any toolpath is divided into the following 7 segments; Plunge, Approach, Engage, Cut Motion, Retract, Departure, and Rapid. The motions that will control how the flat end mill enters and exits the 3D Contoured Groove are the Approach, Engage at the start of the groove, and the Retract and Departure at the end of the groove. The default Toolpath Colors are shown in the Toolpath tab of the CAM Preferences dialog.

Engraving Toolpath Entry Parameters


Engraving Toolpath Exit Parameters


Controlling the Entry and Exit Angles
The Entry and Exit Angles refer to the elevation of both the Engage and the Retract segments of the toolpath. In this case, we want the cutting tool to remain tangent to the Spine Curve to achieve a smooth entry and exit of the groove. In the Entry/Exit dialogs shown above you will see a parameter named Angle (A). This is the angle at which the Engage and the Retract segments connect to the Spine Curve. In both cases, Angle (A) is set to 0 (zero). This keeps the Engage and the Retract segments tangent to the Spine Curve.
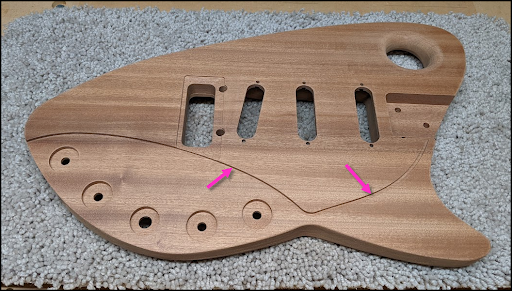
About Jeff Kosmoski
Cool Designs from KOZM Guitars!









More about KOZM Guitars
Thank you for allowing us to showcase your work!
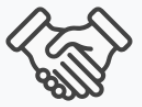