MK Fabrication, a sister company of General Fence, Inc., is a growing full service fabrication shop with mobile capability. Built on quality and customer service, they work on everything from Mining and Heavy Equipment to backyard projects. The ability to manufacture its own custom tooling makes their clients’ jobs easier, faster, and more cost effectuive. Read more About MK Fabrication later in this case stdy.

The RhinoCAM Part
The part features for this case study are mostly prismatic, meaning that they are 2-dimensional with vertical walls. One feature however, has a sloped contour shape. There is a pocket on each side that cuts completely through the part. The part also has five identical sets of features as shown in the illustration below.
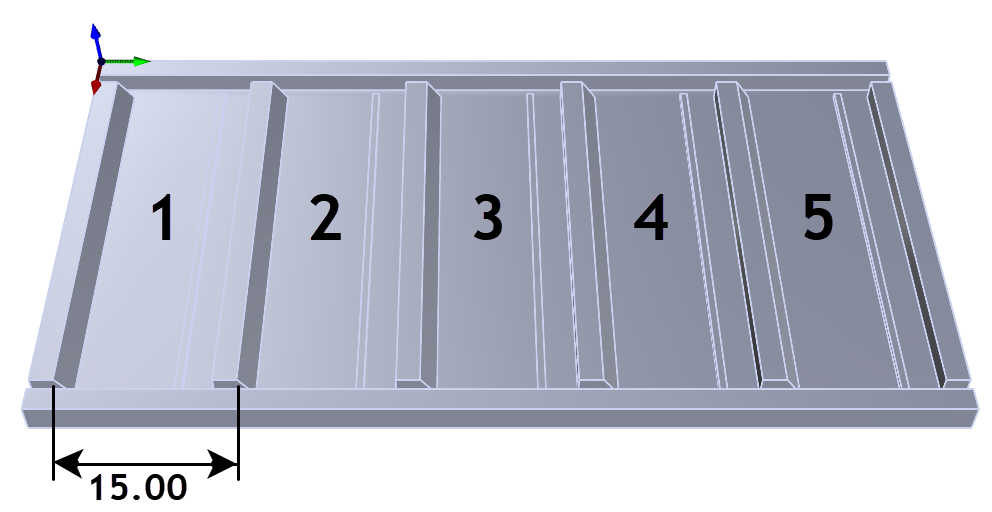
Here we see a 3-dimensional view of the part. It consists of 5 similar sets of features. Each set consists of prismatic shapes except for a sloped feature on the left side, The feature sets are 15.00” apart.
The Cutting Tools
The Machining Job for this project will require three Carbide cutting tools. They are shown below as listed in the Tools tab of the Machining Objects Browser. Two are nearly identical ¾” (0.750”) diameter flat end mills except for the length. One is 2” long and the other 2.5” long. The third is a ¾” (0.750”) diameter Corner Radius Mill (sometimes referred to as a Bull Mill). It is identical to the flat end mill except that it has a 0.250” radius. To be clear, this cutter has a ¼” flat on the bottom and a ¼” radius around its perimeter.



Here we see the list of tools for this Machining job and under each tool is listed the toolpath operation(s) it is used in. We have three cutting tools and six toolpath operations.
The Machining Job
Based on the part features described above, the following toolpath operations are used to machine this part. You will notice from the Machining Job shown below that there is an XY Instance folder that contains all of the toolpath operations to machine the first set of features. The XY Instance folder contains the parameters needed to define the remaining 4 sets of identical features. We will discuss each operation below.

The Machining Job shown above consists of a single Setup 1 followed by a Work Zero. The first operation is 2½ Axis Pocketing. It is used to cut the two traversing pockets. The remaining operations will cut one set of features while the XY Instance folder defines the offset pattern for the remaining 4 sets of identical features.
2½ Axis Pocketing
We mentioned that there are two pockets that traverse the length of the panel on the north and the south ends. These two pockets will be machined first using the ¾” diameter x 2.5” long flat end mill. The pockets are 2” deep and will be machined in 10 cut levels of 0.2” each. The toolpaths for these two pockets are shown below.




The toolpaths shown here have been adjusted for illustration clarity. The parameters described are those for production.
3 Axis Horizontal Roughing
The first operation under the XY Instance folder is 3 axis Horizontal Roughing. It is used to remove the bulk of the material from these features.It uses the 2” long, ¾” carbide flat end mill. It is a Climb cut in an Offset cut pattern, a Stepdown of 0.2 and a Stepover of 60% (of the tool diameter = 0.45”). The cut entry is a 10-degree helix.


3 Axis Horizontal Re-Roughing
The next two items in the XY Instance folder are (Two) 3 Axis Re-Roughing operations and in this case, they are used as roughing and finishing operations. The first re-roughing operation has a Cut Level containment set to leave 0.025” stock and the second re-roughing operation has Clear Flats enabled, effectively finishing the floor and the rib that lies on the floor. The Cut Parameters and Entry/exit parameters are identical for each operation.


2½ Axis Profiling
The next item in the XY Instance folder is a 2½ Axis profiling operation using the same carbide ¾” diameter flat end mill. It adds a cleanup pass to the side wall indicated in the illustration below. The entry and exit occurs in the open pockets that run along the entire part north and south. As I mentioned, there is only one Climb cut level used to clean up this side wall. The Machining Job tree and the profile are illustrated below.


3 Axis Between 2 Curve Finishing
The last toolpath in the XY Instance folder is a 3 Axis Between 2 Curves Finishing operation. This toolpath method is part of RhinoCAM’s Advanced 3 Axis toolset. The operation maps a toolpath between any 2 curves and maintains a consistent stepover distance on the underlying surfaces.
In this case, it is finishing the contour slope surface.This toolpath uses the ¾” diameter x ¼” corner radius mill. The ¼” flat on the bottom of the tool will finish the floor at the bottom of the slope and the ¼” corner radius will finish the sloped surface. The toolpath travels along and between the 2 curves with a constant 0.2” Stepover as it climbs the surface.


XY Instance Operation
In RhinoCAM you can instance toolpath operations if you have identical part features to machine. In our part we see that there are 5 identical sets of part features. They are identified in the illustration below. The toolpath operations illustrated above are for feature set #1. There are 4 more identical feature sets each being 15.00” apart along the Y axis. We are using RhinoCAM’s XY Instance operation to do this.
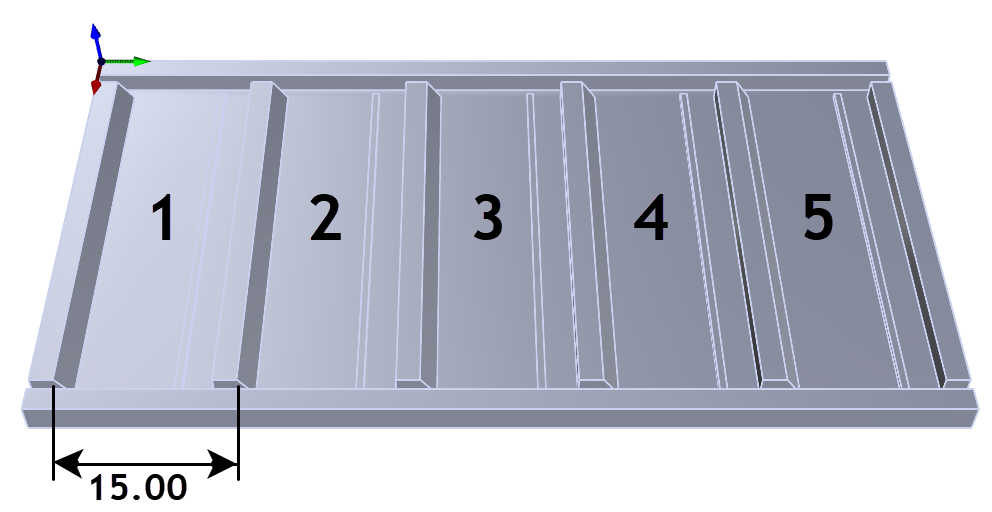
Selecting the XY Instance command from the Other Miscellaneous Operations menu will display the XY Instance Operation dialog shown below. The dialog allows you to enter the spacing of the instances as well as the number of instances. In our case we want 4 copies spaced 15.00” apart along the Y Axis.



When you pick Generate, the XY Instance is created and added to the Machining Job as a folder named XY Instance. You can rename this folder if you like. Now, with the XY Instance created, we just have to drag-and-drop each of our existing toolpath operations into this folder. Then, selecting the XY Instance folder will display the 4 additional instanced copies. This is shown in the RhinoCAM display below.

Post-Processing GCode
During post-processing, each instance of each toolpath operation is commented on in the gcode file as shown below. Optionally, you can post-process one or more specific operations. Options also available to post operations based tool number.


A Special Thanks to MK Fabrication
We want to extend a special thanks to Sparky Polish, Michael Jenkins, and Master Machinist R. Brooks Bench and all of the folks at MK Fabrication for allowing us to showcase their work with RhinoCAM!
Cool project!
Thank you MK Fabrication for allowing us to
showcase your work!


More About MK Fabrication
MK Fabrication modifies and repairs Underground Mining vehicles and other equipment. Our team travels to different locations to do fabrication work to meet customer needs. We are committed to getting the job done on time and accurately. Our new building is in the process of being built, expanding our capabilities and enabling us to serve a wider range of customers. The future at MK Fabrication is bright.

MK Fabrication Welding Certifications
MK Fabrication is ANSI/AWS certified in the following welding applications:
- Gas Tungsten Arc Welding of Austenitic Stainless Steel
- Shielded Metal Arc Welding of Carbon Steel
- Standard Welding Procedures Specification
MK Fabrication Capabilities
Here are just a few of the capabilities that MK Fabrication specializes in:
|
|
More about RhinoCAM
RhinoCAM – MILL is available in 5 different configurations (Express, Standard, Expert, Professional and Premium). The part shown here was programmed using the Professional configuration. Here are some additional details about each of the available configurations. For the complete features list, visit the RhinoCAM Product Page.
- VisualCAD/CAM MILL Express: This is a general-purpose program tailored for hobbyists, makers and students. Ideal for getting started with CAM programming. Includes 2 & 3 axis machining methods. Includes ART & NEST modules as well!
- VisualCAD/CAM MILL Standard: This configuration includes everything that is in the Express configuration plus additional 2-1/2 Axis, 3 Axis & Drilling machining methods. Also now includes 2½ Axis Turning!
- VisualCAD/CAM MILL Expert: Suitable for 4 Axis rotary machining. Includes the Standard configuration, plus 4 Axis machining strategies, advanced cut material simulation and tool holder collision detection.

- VisualCAD/CAM MILL Professional: Ideal for complex 3D machining. Includes the Standard and Expert configuration, plus advanced 3 Axis machining strategies, 5 Axis indexed machining, machine tool simulation, graphical toolpath editing and a host of other features.
- VisualCAD/CAM MILL Premium: Tailored for complex 3D machining with both 3 Axis and full 5 Axis methods. Includes the Standard, Expert and Professional configurations, plus 5 Axis simultaneous machining strategies.

Add Your Heading Text Here
Lorem ipsum dolor sit amet, consectetur adipiscing elit. Ut elit tellus, luctus nec ullamcorper mattis, pulvinar dapibus leo.


Add Your Heading Text Here
Lorem ipsum dolor sit amet, consectetur adipiscing elit. Ut elit tellus, luctus nec ullamcorper mattis, pulvinar dapibus leo.








